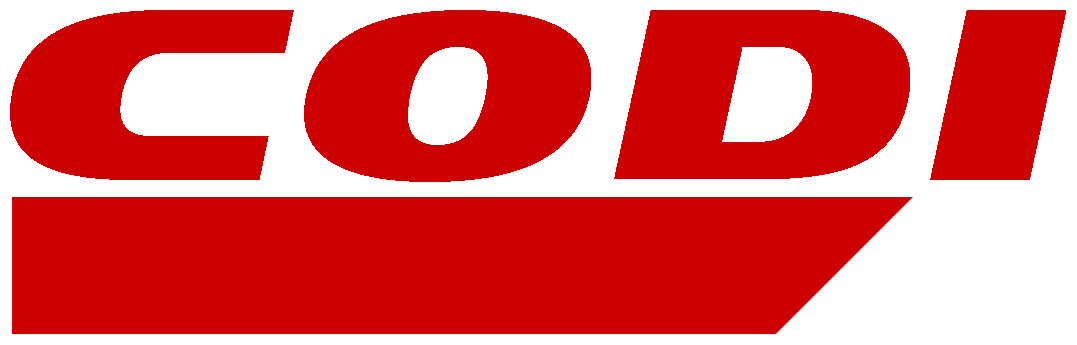
Benefits of Counter Pressure Filling Craft Beverages using a Micro Canning System
Quality, Quality, Quality
Quality Into The Can, Quality Out of The Can
Quality Design
- What Materials is the canning system made from?
- Counter Pressure vs Open Air Filling
- Counter Pressure Filling brings the product into a filler bowl and pressurizes it to the optimal pressure for canning. This is critical for lightly carbonated products.
- Ability to reduce dissolved oxygen by properly purging the can prior to filling
- Positive Positioning Seaming for Nitro Dosing to add pressure to the can.
- All other small line suppliers use pneumatics to index cans into the seaming operation which when liquid nitrogen is applied in turn doesn't keep can firmness the same. This is because liquid nitrogen boils off at 700 times its volume. Having the same time from liquid nitrogen dose applied to the can being seamed is critical for package consistency.
- Mechanical Engagement of critical Seaming Operations
- Use of pneumatics are great for reducing costs but it also brings up the potential for out of specification seams on cans.
Quality Cleanablilty
- Cleaning a Canning Line with 180 degree caustic is key to keeping a machine clean.
- Minimum flow rates of 3 to 5 gallons per minute through all lines removing buildup on hoses.
- Recirculation of Chemicals to increase contact time of cleaning without increasing costs of chemicals
Quality Canning
Dissolved Oxygen in beverages can shorten beverage shelf life. Counter Pressure Filling is the best solution to getting lower Dissolved Oxygen because the beverage is kept in solution and filled under pressure with limited exposure to atmosphere. With a Gravity Fill, oxygen is being en-trained into the beverage throughout the filling process.
Oxygen trapped in the package contributes to flavor degradation in beverages. The greater the amount of oxygen, the greater the flavor degradation. The oxygen content of a package can be measured to determine if the origin of the oxygen is from the headspace, or from the filling operation.
Oxygen is introduced into the package in two places: during filling or in the headspace through incomplete fobbing. Filler oxygen can come from air already in the beverage or from air trapped in the can or filler tubes during filling. Headspace oxygen comes from air trapped in the headspace after the end is applied. Because the partial pressures of gases in the headspace and the liquid are not at equilibrium immediately after packaging, all packages should be shaken before measuring dissolved O2
© 2016